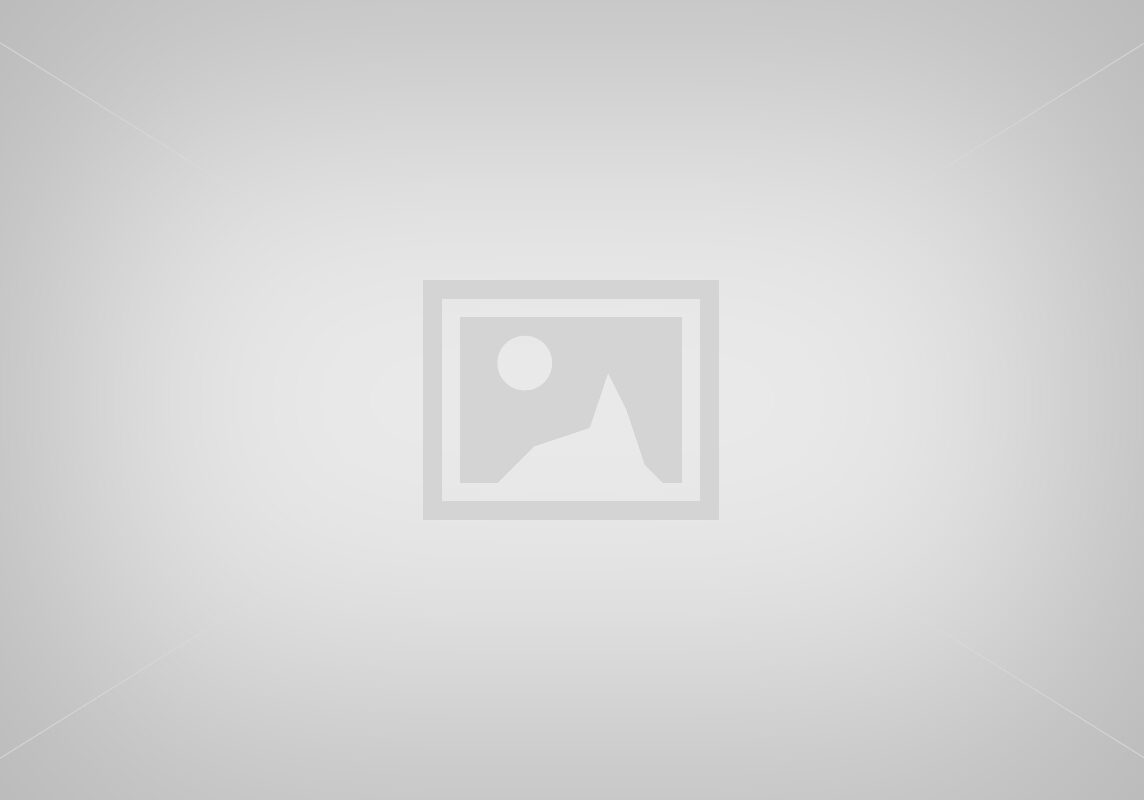
More on Mineral Wool
I got some great comments last week when I posted a short video about mineral...
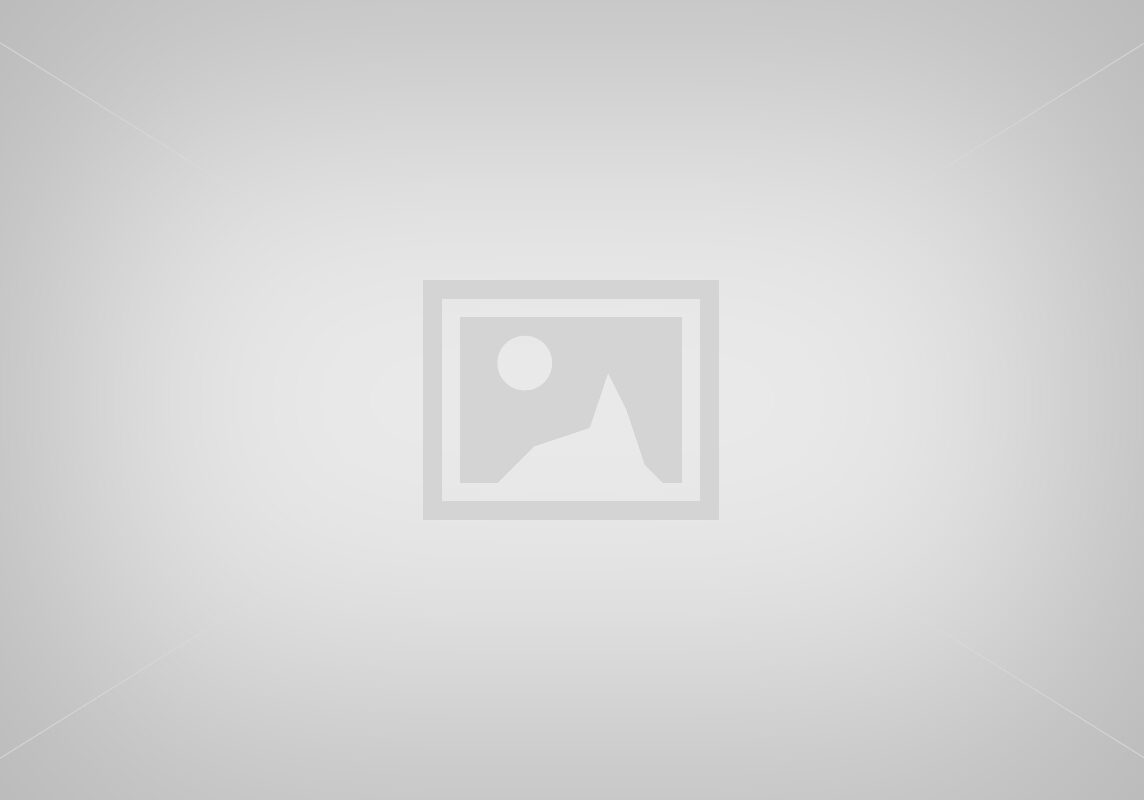
Join the Build Better Crew: Firestop Insights & Community
Tomorrow is another gathering of our Build Better Crew. If you’re an architect, building official,...
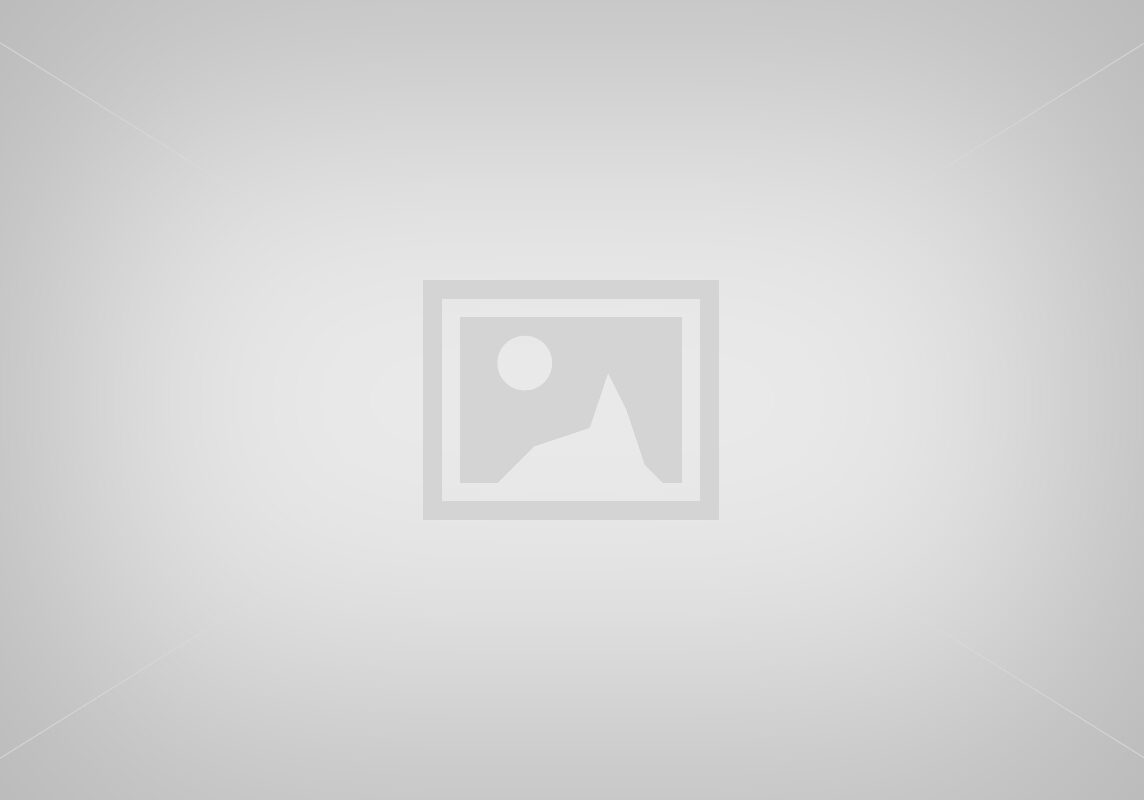
2.5 PCF Mineral wool
Are the contractors on your project still struggling to source mineral wool? If so, please...
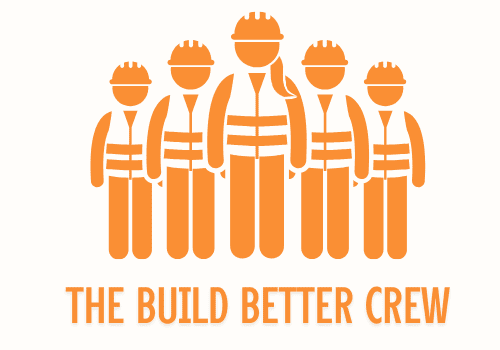
Join The Build Better Crew
It’s not too late to Join The Build Better Crew. A place where you can...
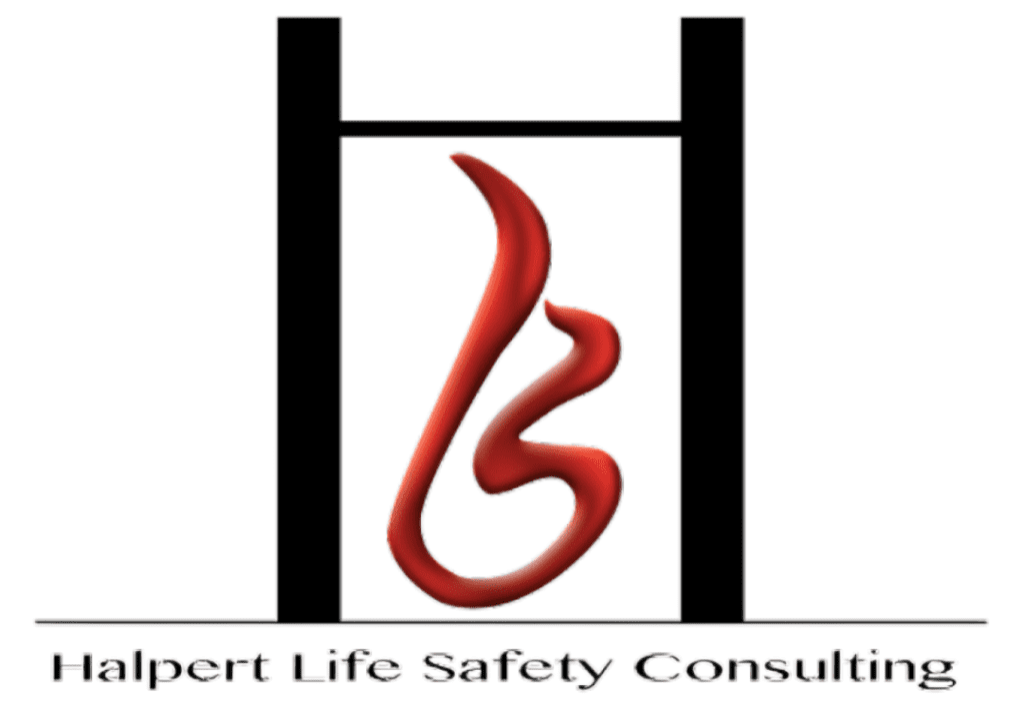
Renovating Low-Income and Disabled Housing: An Amazing Opportunity
I've received an invitation to collaborate on a project in NJ that involves renovating housing...
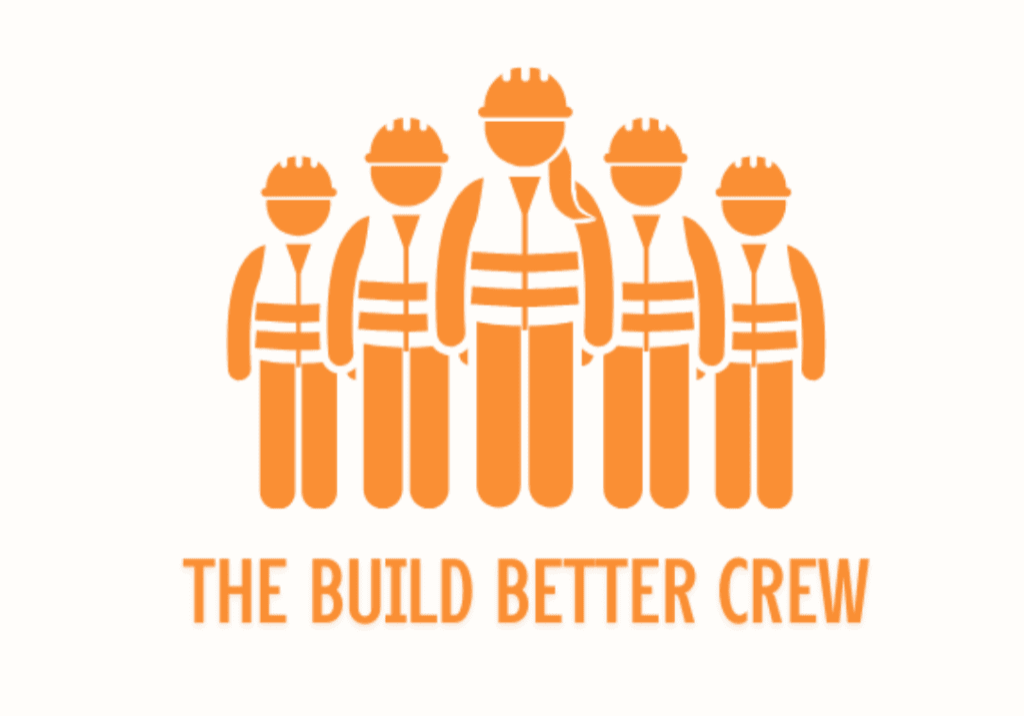
Where do you go for firestop and passive fire protection advice?
Where do you go when you have questions related to firestop and passive fire protection? It...