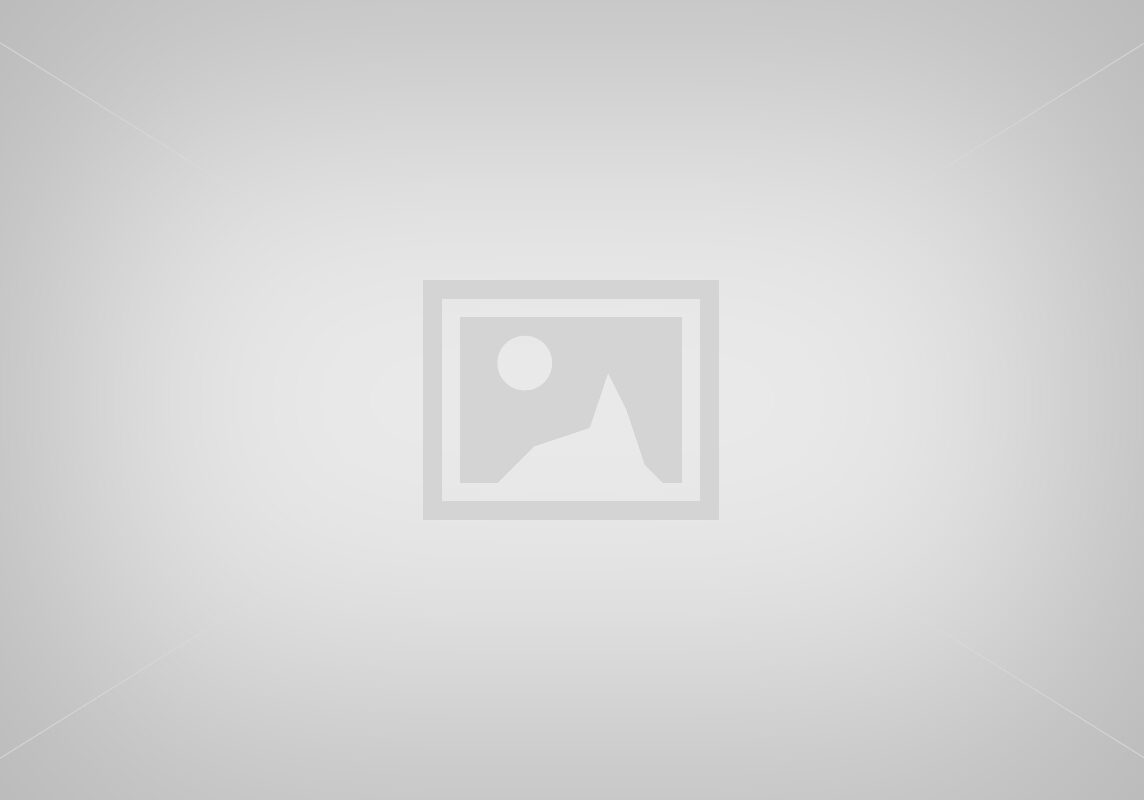
Prohibited Penetrations- If you need one.
Does your project have pressurized stairwells? If so, prohibited penetrations could impact your next project....
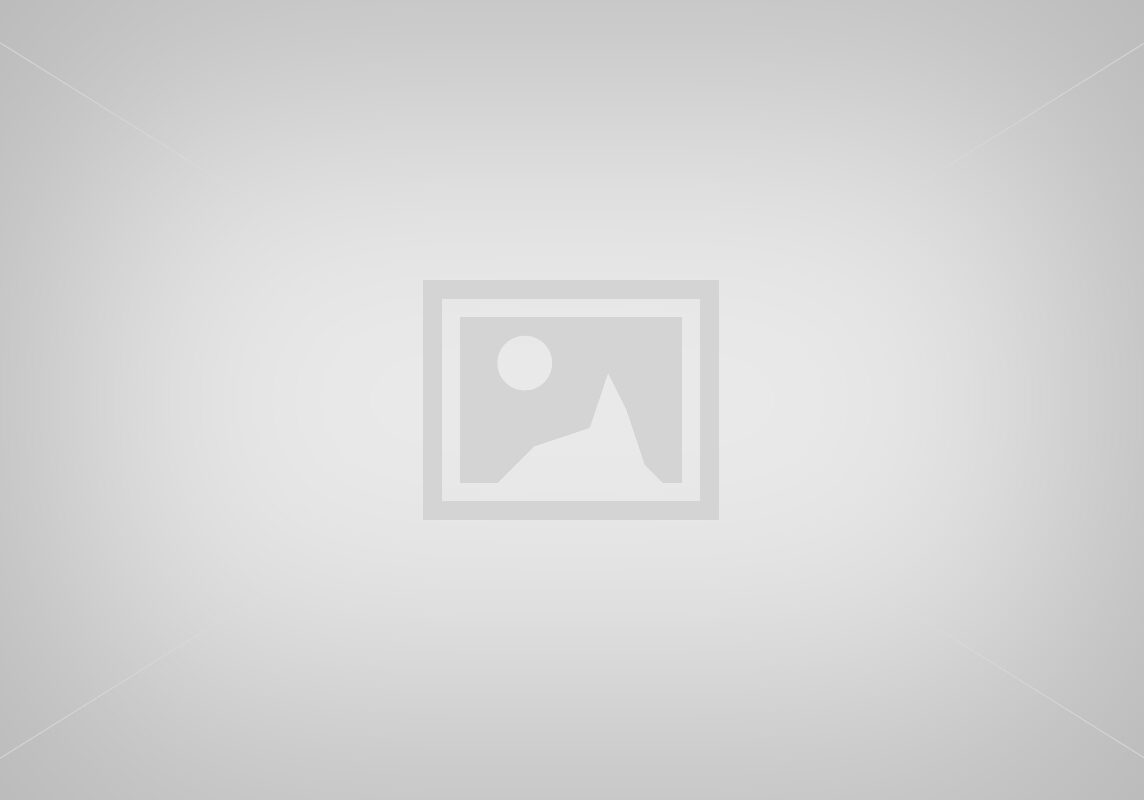
Penetrations in gypsum shaft walls
Does your project have gypsum shaft walls? If so, please DO NOT make this mistake....
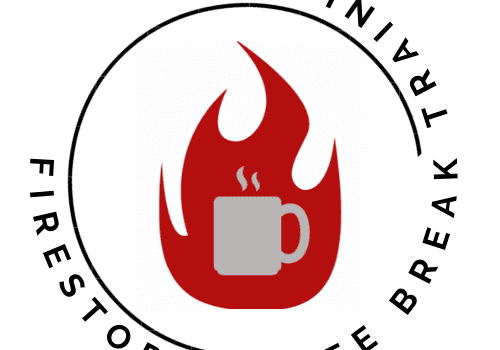
Modern furniture
Modern furniture burns much faster than furniture used when our current fire test standards were...
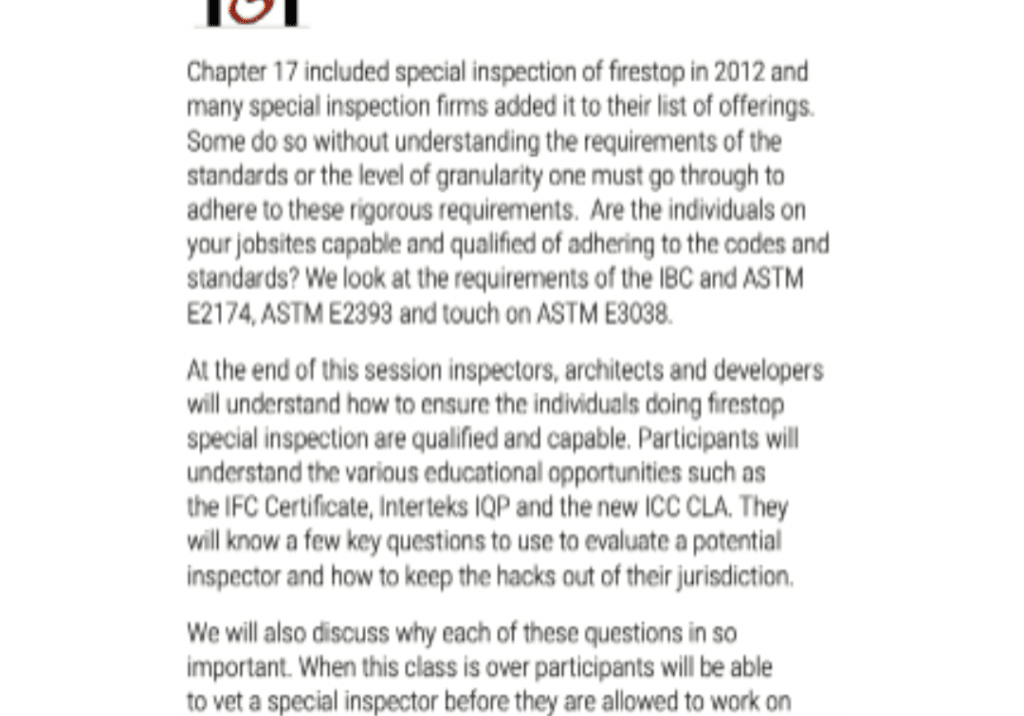
Educode- Firestop Special Inspection
Are you coming to Educode? Join me Wednesday after lunch for this class. #BuildBetter #FirestopCoffeeBreakTraining
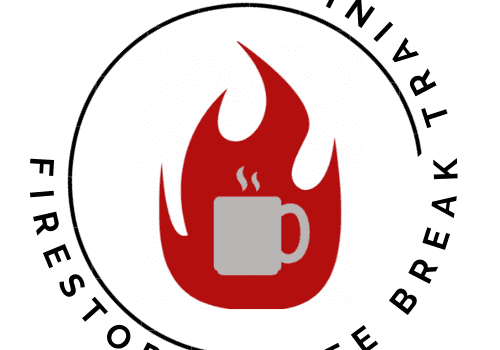
E-Bike Fire Risks: A Growing Threat to Safety
If your family has one of these, even if it’s new, be aware of E-Bike...
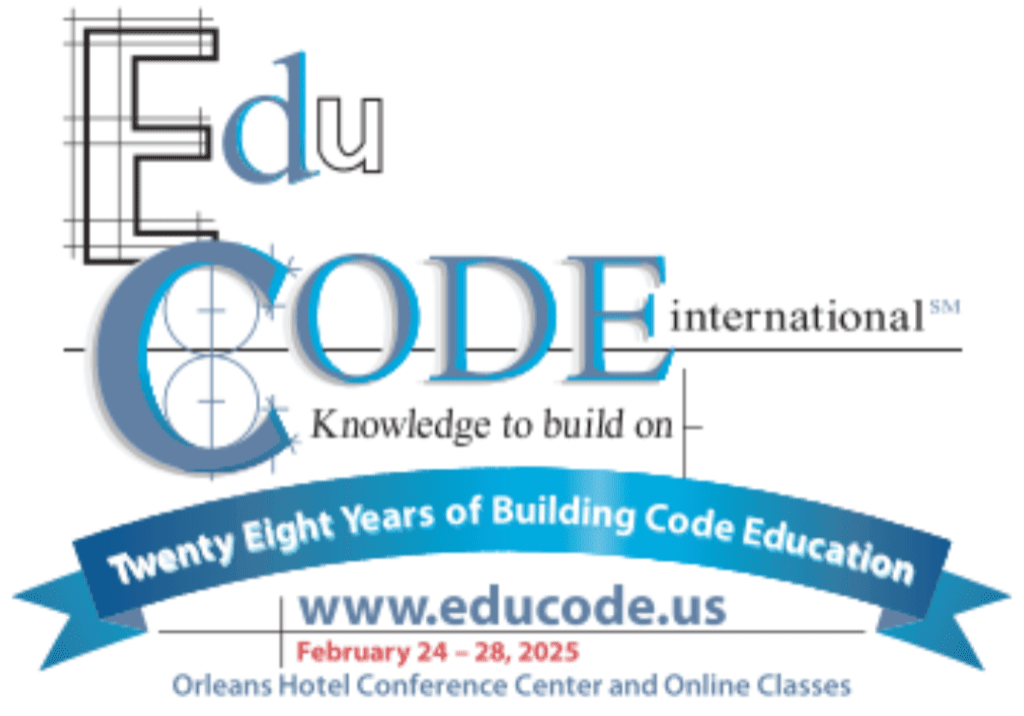
Be careful what you ask for…
You have heard that before, right? Well, I was teaching a class last year, and...
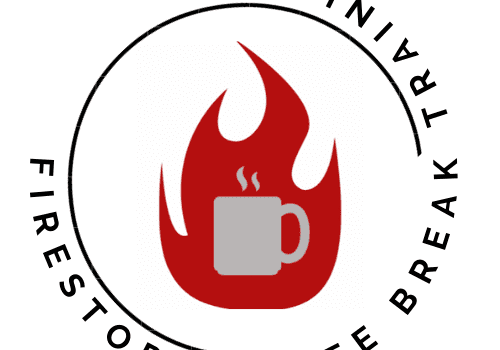
Note to architects
If you are an architect or you support architects in ANY WAY, please read this...