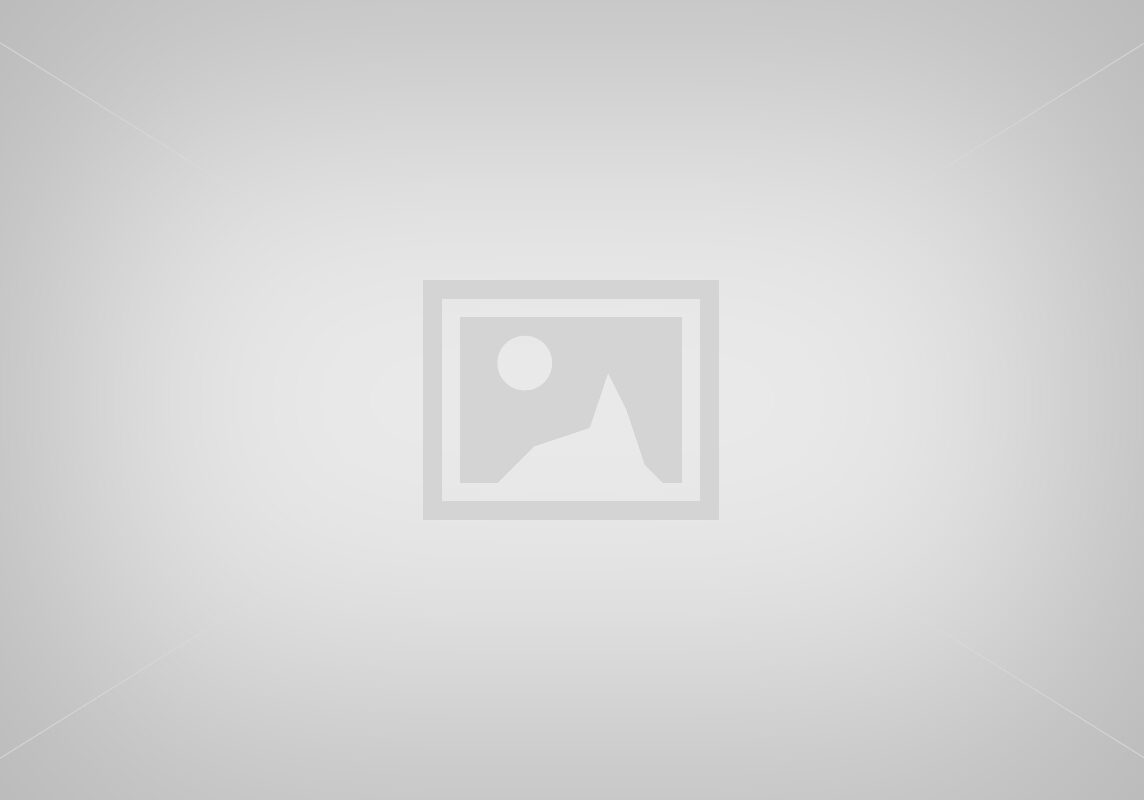
Fired-Up Firestopping: CEUs for Code Pros
If you're looking for CEU’s and you take DCA classes through Rutgers, check out this...
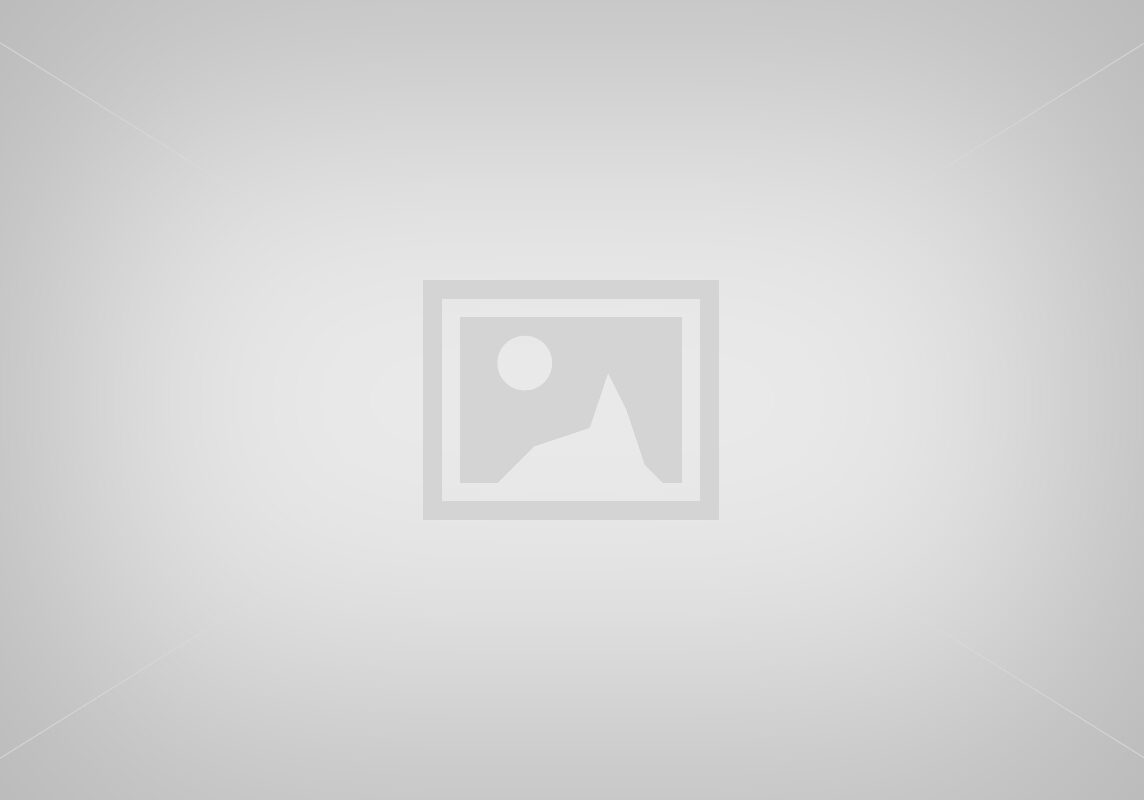
Where do you go for Firestop Help?
Where do you go when you have questions about firestop? If you have a question,...
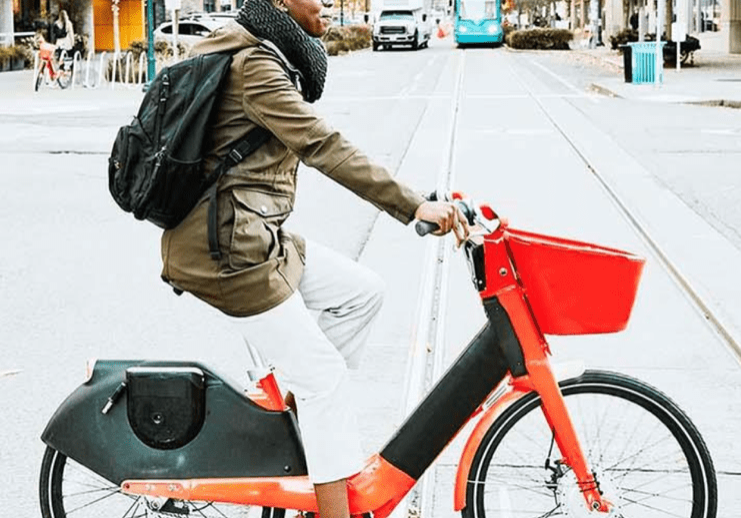
Lithium Ion batteries
Does anyone in your family have e-scooters, e-bikes and other Lithium Ion batteries, even your...
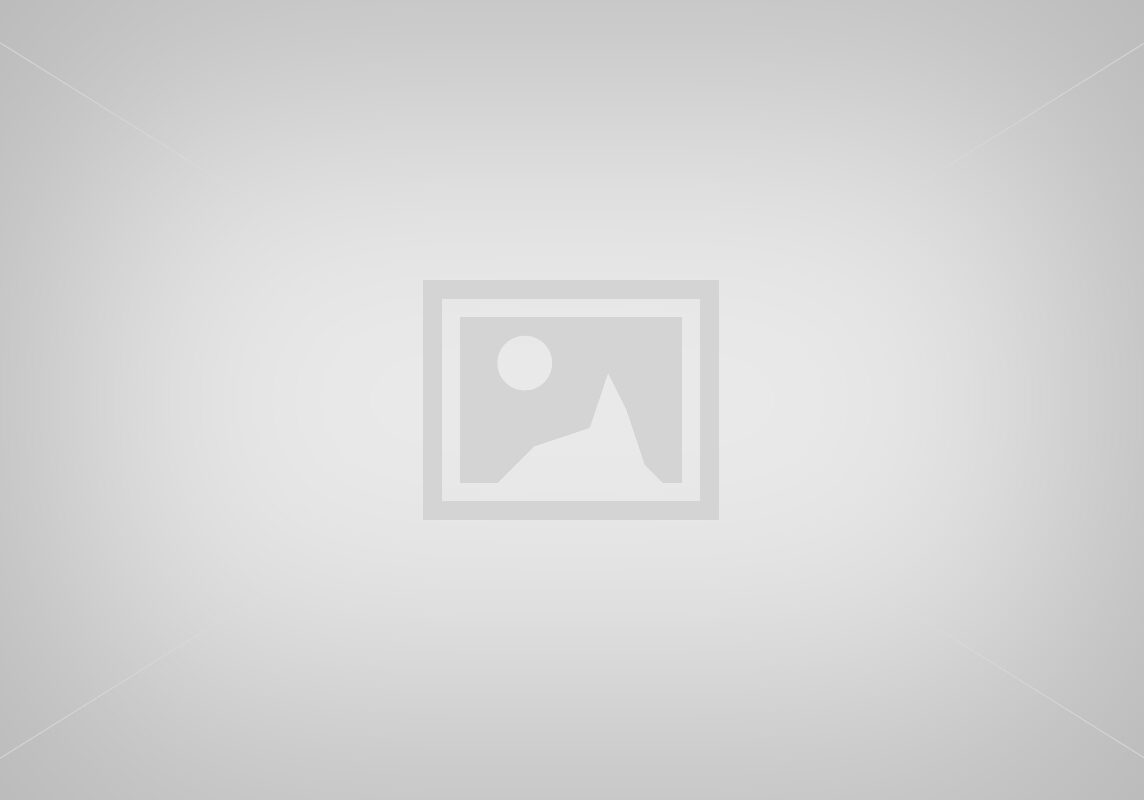
Does your project have horizontal rated lids?
Does your project have horizontal rated lids? I’m not talking about rated ceilings that are...
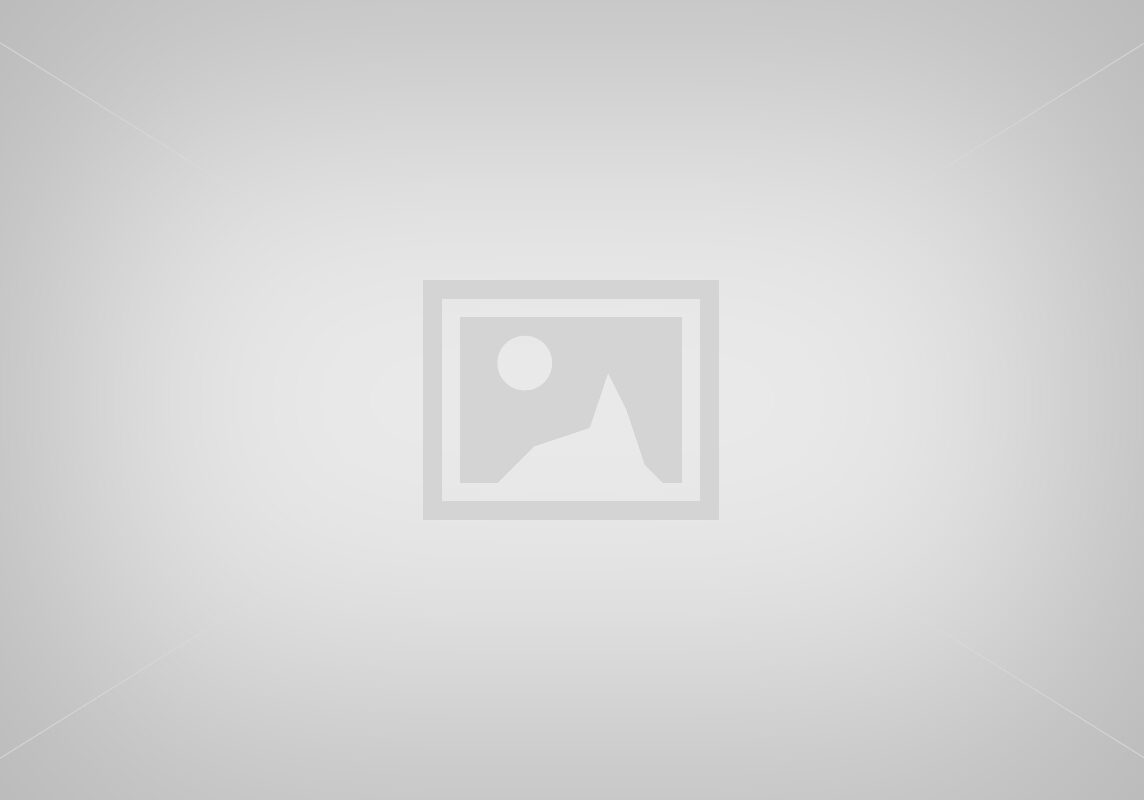
What you don’t know about Rated walls, might be a problem.
https://www.ul.com/thecodeauthority/news/update-gypsum-area-separation-wall-designs Here is a great article from UL about rated walls. Have a read and...
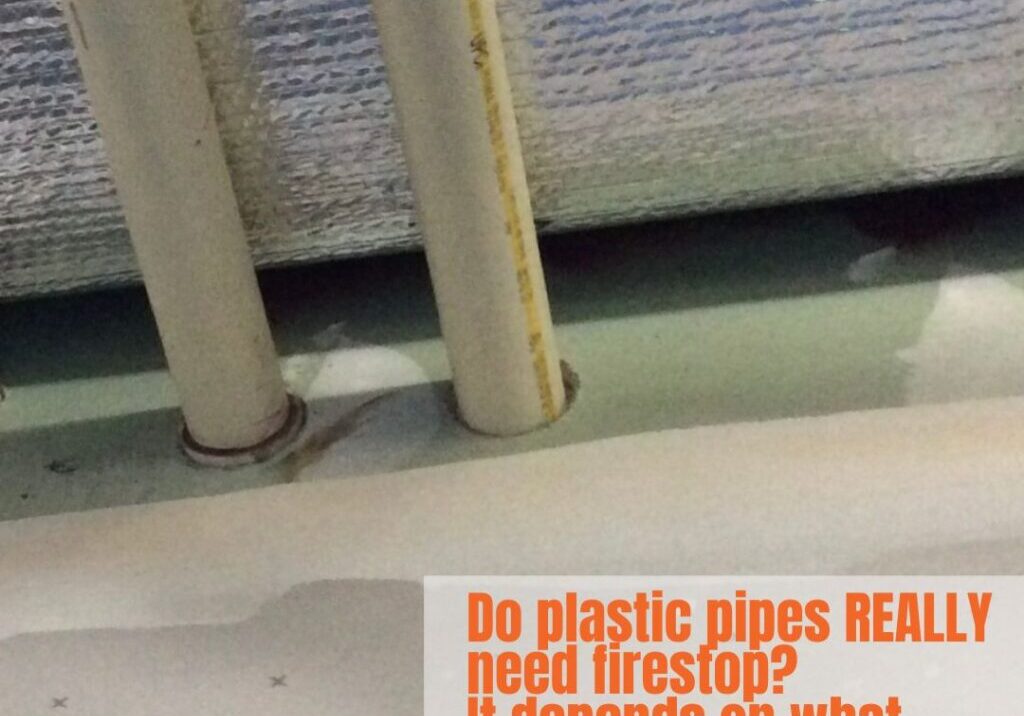
Fire Safety Gaps: US vs. Europe on Plastic Pipes in Walls
What would you say if you saw a 5” diameter plastic pipe through a gypsum...