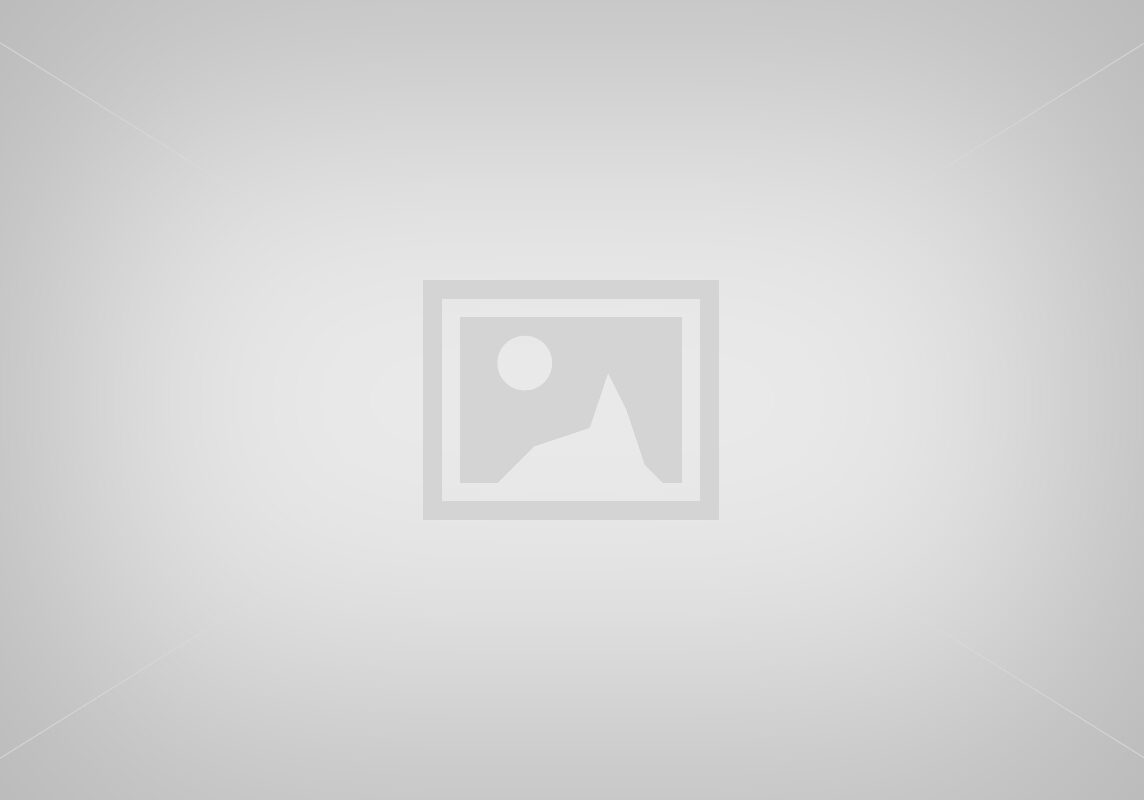
How to tell if you have the right special inspector looking at firestop
If you are a developer or a building official it is important you understand the...
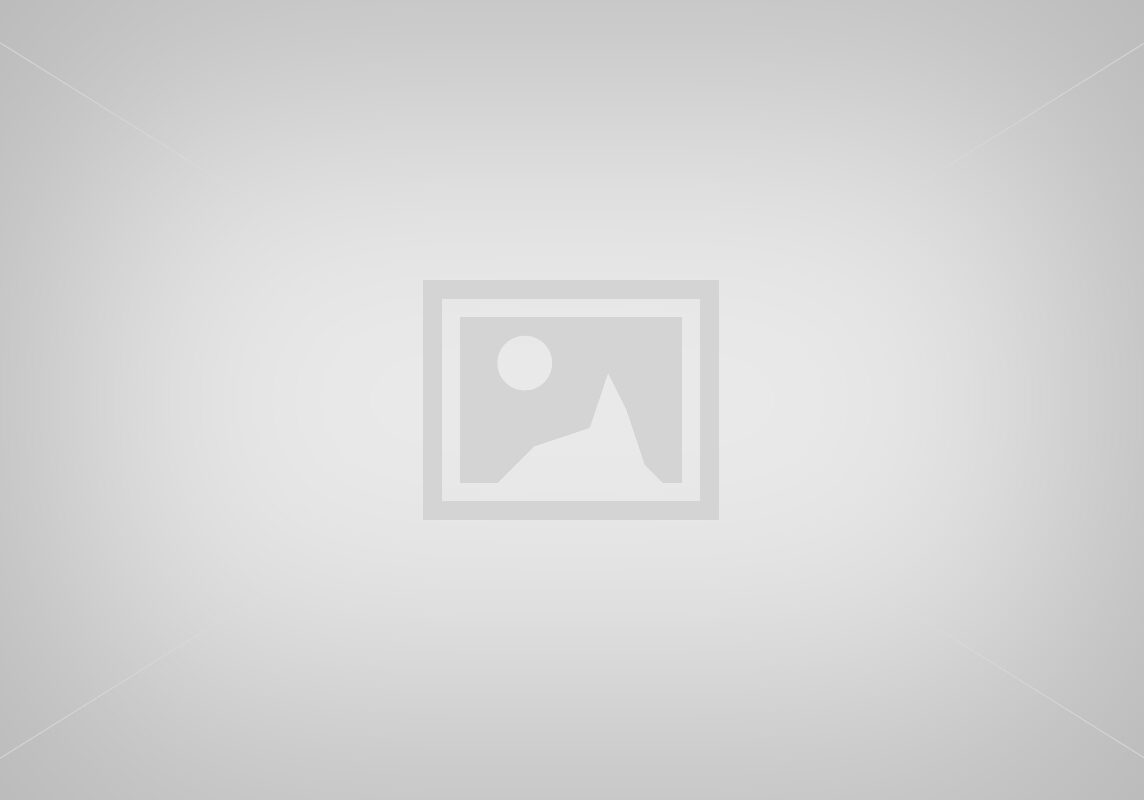
Do you need a special inspector on your project?
What types of projects do you work on? Are you required to have a special...
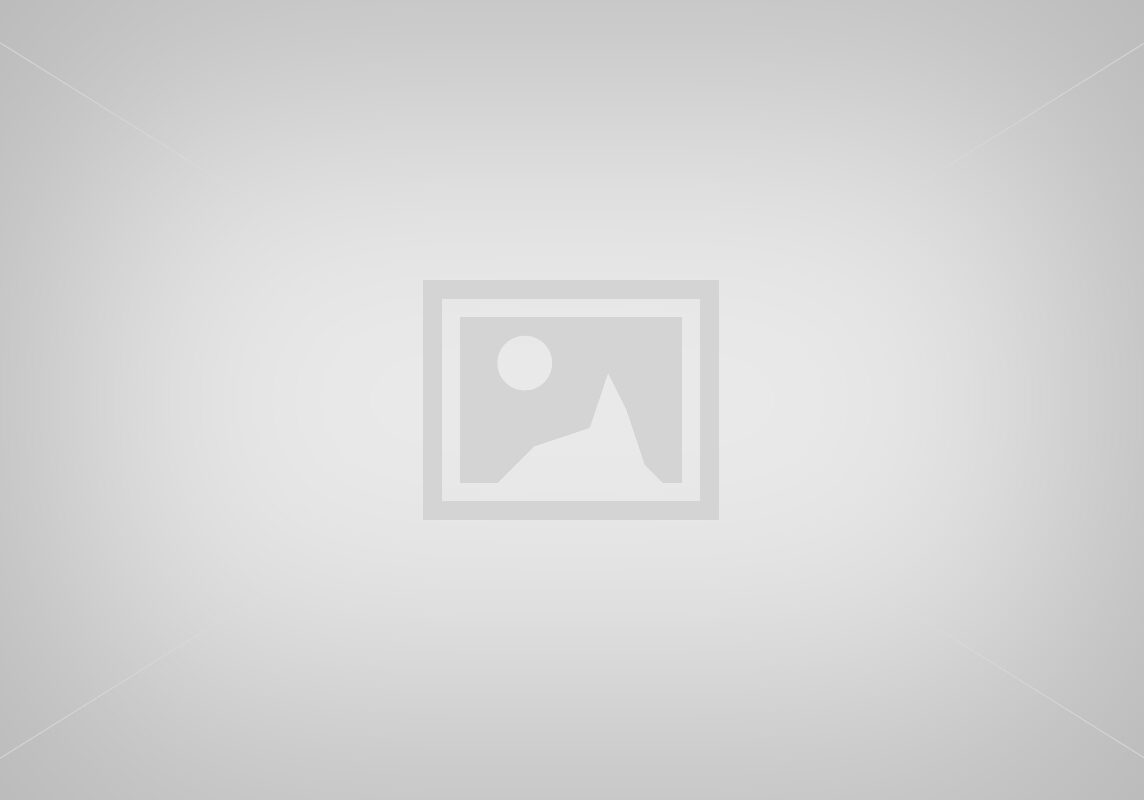
Changing building codes
How do you stay on top of changing building codes? When there are standards written...
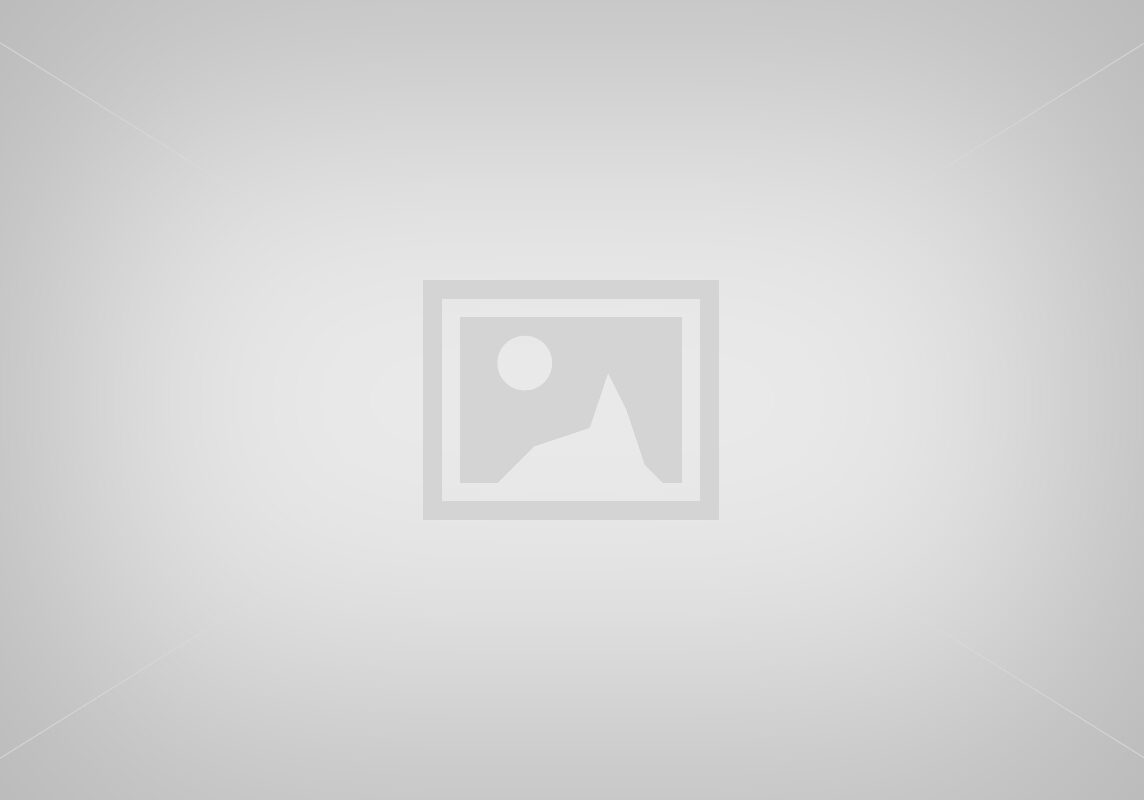
EQUALS Global Partnership’s webinar series, Uplifting Women
Today’s the day. I hope you will be joining me at 11:00 EST for the...
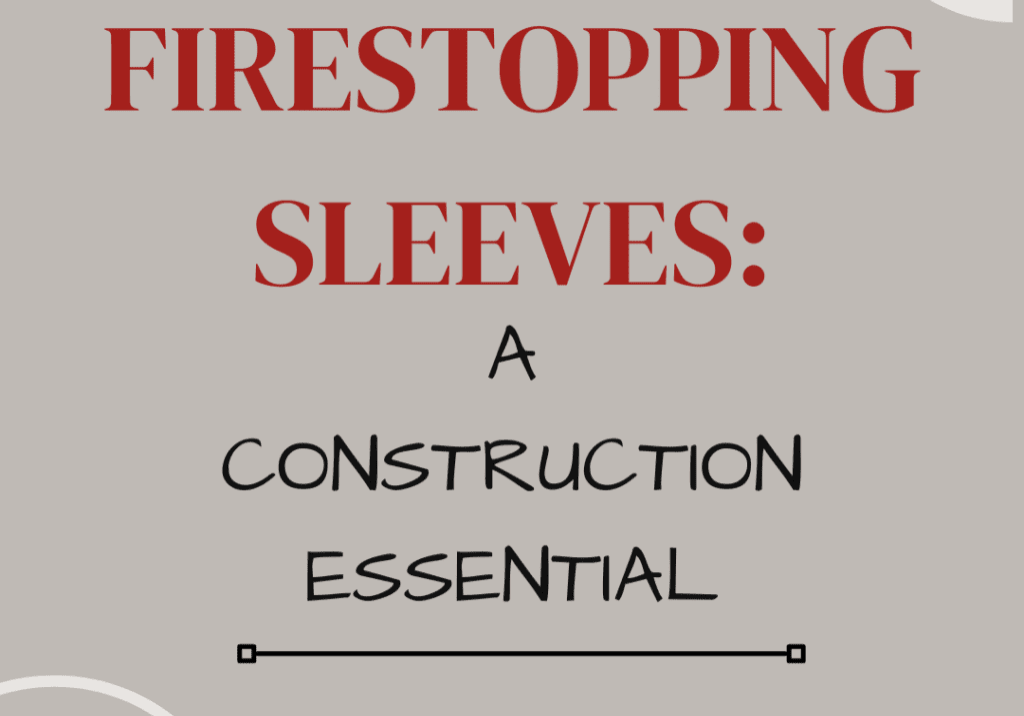
Firestopping Sleeves: A Construction Essential
Firestopping Sleeves play a crucial role in various projects, and it's essential to understand their...
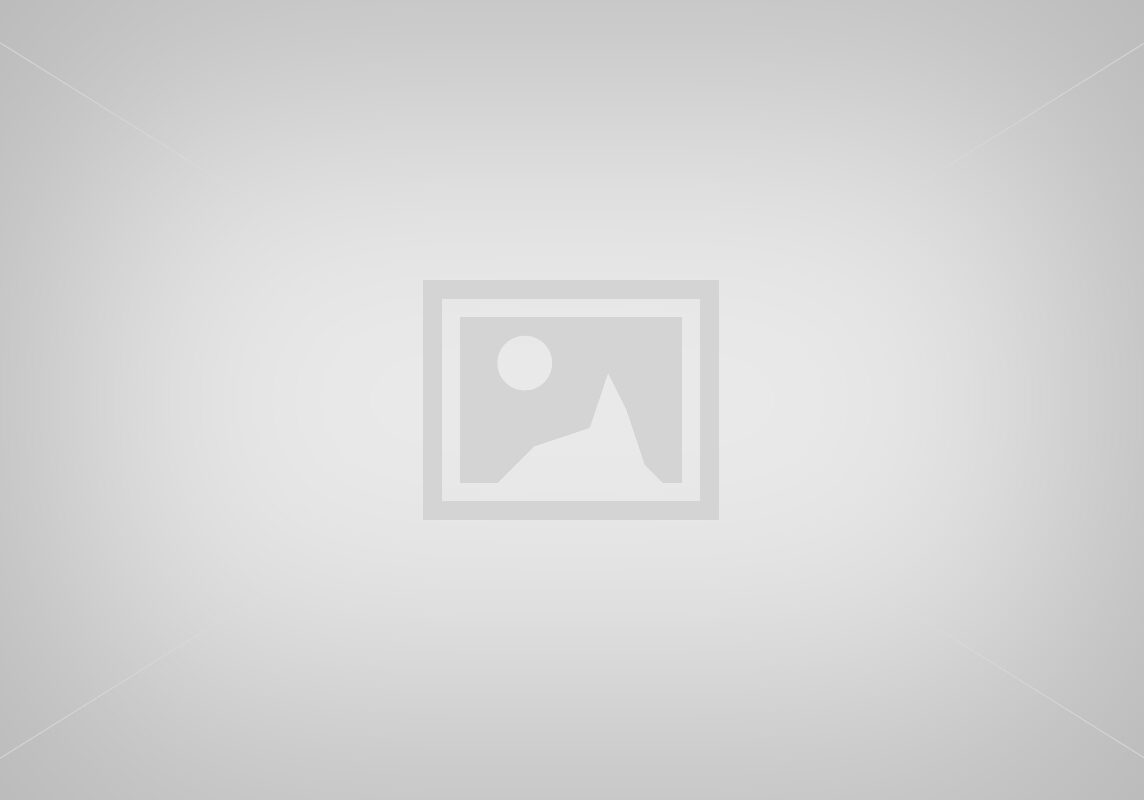
NEEDLESS SLEEVES IN FIRESTOP AND A STORY ABOUT A ROAST
One of my favorite questions to ask architects during our training is, WHY DO YOU...